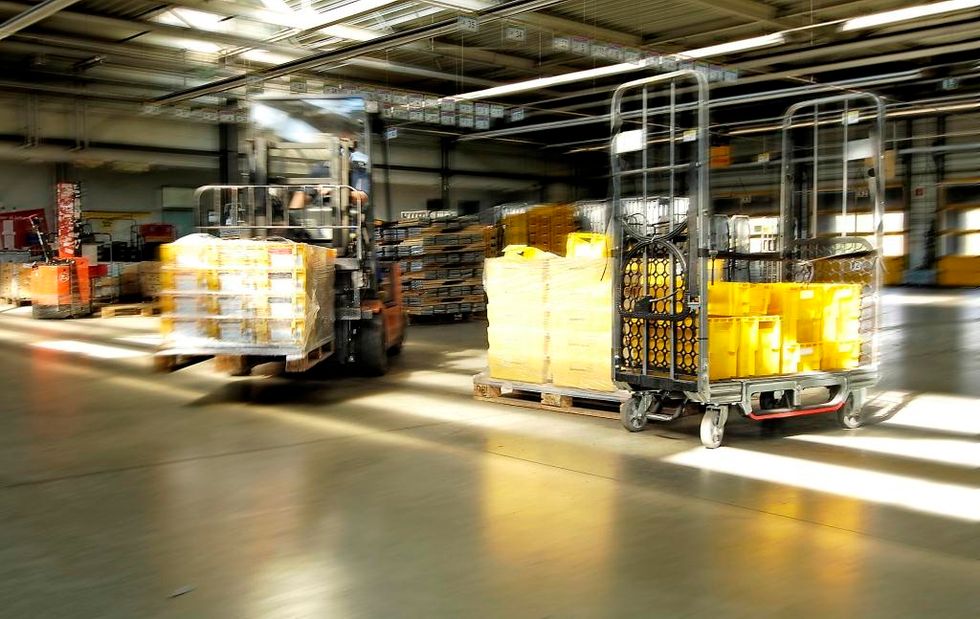
Ten Tips to Running a Safer Distribution Center
Penske Logistics is a leader inwarehousing and distribution center optimization. The company safely manages over 19 million square feet of warehousing space for market-leading companies around the world. Eric Hepburn, vice president of distribution center management for Penske Logistics, offers these tips, in no particular order, gleaned from personal experiences over the last 15 years:
1. Take safety personally and make it personal: Penske has gone through an enterprise-wide rededication to safety. Our safety numbers are strong but we have challenged associates to aim for zero injuries. In doing so, leading indicators fell at a greater rate than ever before.
2. Never miss an opportunity to talk safety with your associates: What’s the first thing you say to a warehouse associate when greeting them? If safety isn’t mentioned in the first minute, you’ve wasted an opportunity. Open with it and close with it. A conversation might go like this: “Hey John, how is it going today? Safe day so far? Keep up the good work and be safe.” It seems easy when it’s written but making it a practice takes a conscious effort on the part of a manager.
3. Even at its best nothing is foolproof: Accidents are still going to happen - it’s all about limiting the chances for one to happen. Make sure you set the tone with your team by starting the day with a safety briefing. Know your numbers. When you know the facts and numbers your team will see the importance you place on running a safe workplace.
4. Invest in people and their safety: It requires investment but every penny spent trying to prevent an accident is better than any expense dealing with the results of an accident.
5. Talk safety from the initial interview: Make it part of the first interaction with any new associate. If they hear it on the day they’re interviewed they will know to take it seriously when accepting the job.
6. Extend the boundaries of your safety zone: Provide a safety briefing and one-page document to drivers with inbound loads or who are on-site to pick up outbound loads. They are not as familiar with the building, dock doors, etc. Brief them so they operate as safely as one of your own associates.
7. Imagine having to inform an associate’s family that there’s been a serious accident: Although I hope no one who reads this ever has to do it, trust me when I tell you having to inform an associate’s family member there has been a serious accident will instantly recommit you to focus.
8. Don’t take no for an answer: People can and will change. Don’t let your team be comfortable with their performance regardless of how good their safety numbers might be. There is always room for improvement.
9. Promote safety through incentives: I’d rather provide a $100 a quarter safety bonus to 100 associates than fund one $10,000 claim for careless behavior that placed people in danger. Budget for it during the planning season and know you’re going to use it to reward great behavior.
10. Provide immediate feedback when you see an unsafe act: Don’t walk past someone doing something unsafe. Stop and provide counseling to the associate rather than seeking out their supervisor to discuss the issue.
By “Move Ahead” Staff